Q&A With HELU: Design Considerations for Dynamic Applications - Part 3 of 3
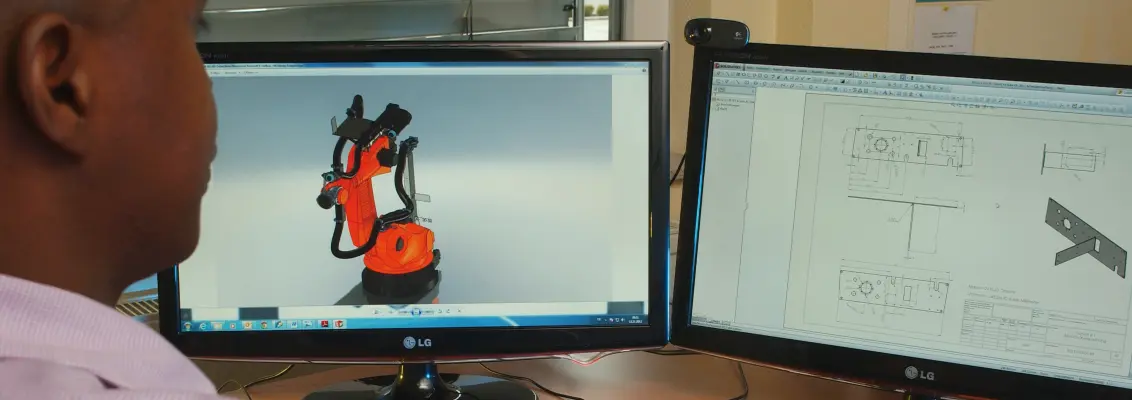
In this final of three Q&A sessions Keith Wilkerson, Business Segment Manager for Robotics and Automation, will discuss some design best practices as well as the common mistakes and failure modes associated with dress pack installations he has encountered over the last 20 years at various OEMs and end users.
Q: What are some of the mistakes you see made with the engineering design of robotic dress packs?
A: The biggest one I see is using drag chain rated cable as part of the fill package, which is a great example of a good cable being used in the wrong application. Once you get beyond a commodity cable, like VNTC, and into premium cables, the robustness of the cable will move up the performance scale. This does not mean all “flexible” cables can be used in all applications. Cables used in drag chain applications can withstand limited amounts of torsion. However, most manufacturers would not advise the use of those types of cables simply because testing has not been performed and, more importantly, the design/construction of drag chain and torsion-rated cables are different i.e. the lay length and lay types discussed in part one of this Q&A white paper. Another design mistake I see that will wreak havoc on the dress pack is not allowing enough cable and conduit past the exit point of the spring return system. The robot is much stronger than the polyamide material that conduit is typically made of. Therefore, if the conduit is too short the robot will eventually stress it to failure. I’ll discuss the axis values shortly.
Q: What are some of the best key practices when designing and building dress packs?
A: Let’s first discuss why we even use dress packs. Wouldn’t it be easier to just zip tie or use hook and loop securing methods for the cables and hoses? Believe it or not, I have seen this in my travels! Dress packs are installed to secure, manage, protect and guide the internal components through the robot’s work cycle, millions of times. When designing a new dress pack we want to understand the full scope of the application. So, we will ask a lot of questions and I do mean a lot! However, this level of detail ensures we get the design correct in the digital world before it becomes a disaster in the real world. You should always consider a dress pack with some sort of mid-package interface. Installing a dress pack that runs from the base all the way to the end-of-arm-tooling (EOAT) will become a maintenance and replacement challenge. Axis three to axis six is where the cables and hoses will see the most mechanical stress and therefore the most failures. We like the swing arm philosophy, which designs a bulkhead connection point on the swing arm between axis two and axis three. This makes for a quick change out, reducing down time. As a side note, having on-hand critical spares of finished dress packs is a great hedge against down time that we highly recommend. We keep a vast inventory of components in our central warehouse if that is not an option.
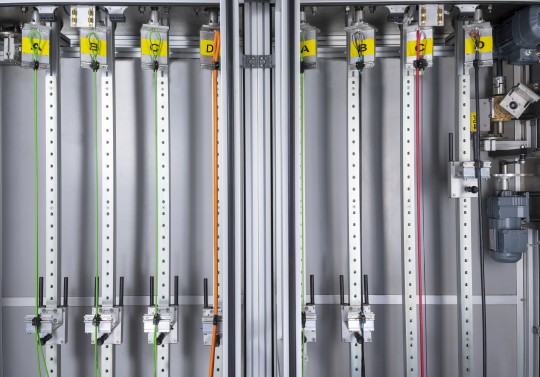
Q: How important is it to understand the +/- values for each degree of freedom during the design phase?
A: Let’s think of this from a fairly simple perspective. If you have a point of rotation, like axis one for example, that moves from its ready position to +123° then back to a -176°. The distance traveled is different than a set of programming parameters where the +/- would be 20° less. Keep in mind that on axis one the mechanical forces are rather minimal compared to what the dress pack and its fill package will experience where the real action is – axis three to axis six. Add in the rotational speeds of 150°/s or more and you have a real mechanical engineering challenge. Bottom line is it’s simply not advisable to design around a robot’s ready position and not take into consideration how the robot will be moving through space. We understand that some things change between design and commissioning. So, I will mention post install optimization. HELUKABEL offers this as a “thank you” service 90 days after delivery of our plug-and-play systems. This service is offered in order to “tweak” the performance of our dress packs and catch any potential issues with the install before they become the bane of the maintenance technician’s existence.
Q: What are some of the main dress pack failures you see in the field?
A: About 85 percent of dress pack failures and down time are related to the cables and hoses. Unfortunately, this is the norm due to the high mechanical stress these components see across millions of cycles. The best way to combat this is by implementing preventative measures at regular intervals. A simple visual inspection, if done consistently, can reveal potential issues before they become failures.
Q: What are some of the best indicators that an end user can look for to determine if their dress pack/fill package is beginning to fail?
A: As mentioned before, cables and hoses fail most often. Indicators would be typical and as expected. Electrical intermittency, data drops and possibly fluid leaks are all good clues. These may manifest in the cell running at short intervals between program interruptions. There are a few mechanical indicators as well. Conduit begins to split and/or tear. Impact protectors wear to the point of actually catching on the robot arm or joint, which may impede the intended path of movement for the conduit. The conduit sags or has more slack than when it was installed. Keep in mind dress packs are installed to secure, manage, protect and guide the internal components through the robot’s work cycle. If you have dress packs that are not accomplishing these fundamentals, then it may be time to have a wellness check performed by an outside expert.
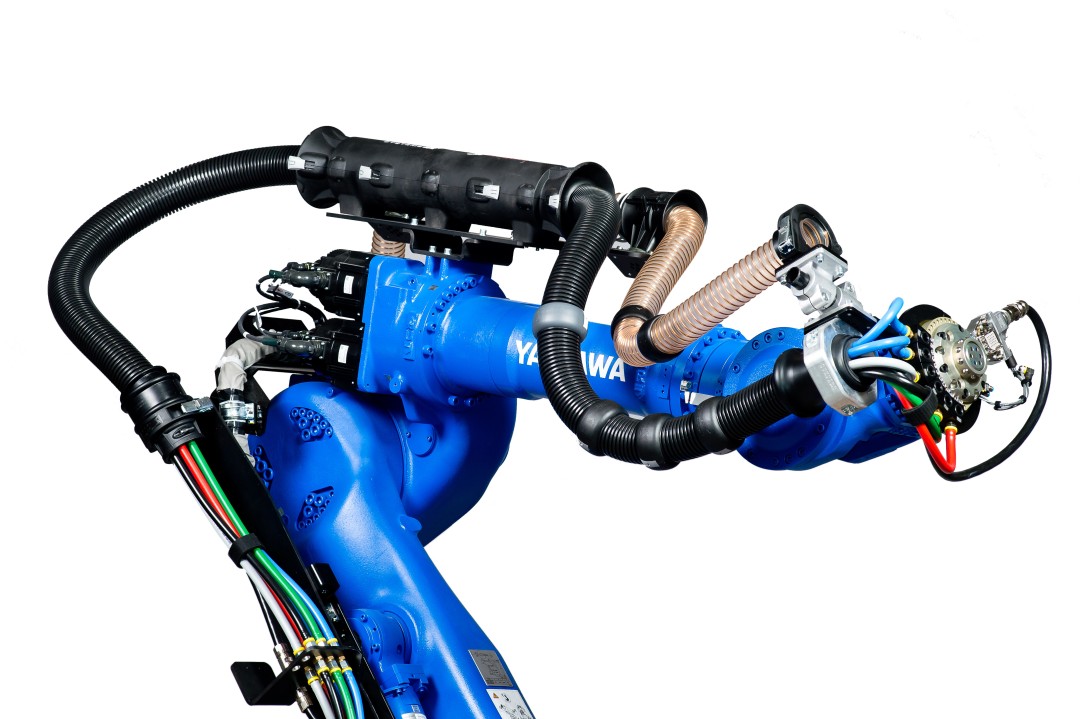
If you would like assistance with a new robotic dresspack design or would like to discuss scheduling a wellness check for a a dress pack currently in use at your facility click here or email us and one of our technical experts will contact you directly.
If you are interested in learning more about HELUKABEL and the broad product portfolio we offer click here for our digital bookshelf.
Click if you missed the first and/or second of the three Q&A sessions focused on cable design for dynamic applications and drag chains.
ARTICLE DOWNLOAD
Click here to view this article in our digital download center.