Q&A With HELU: Design Considerations for Dynamic Applications - Part 2 of 3
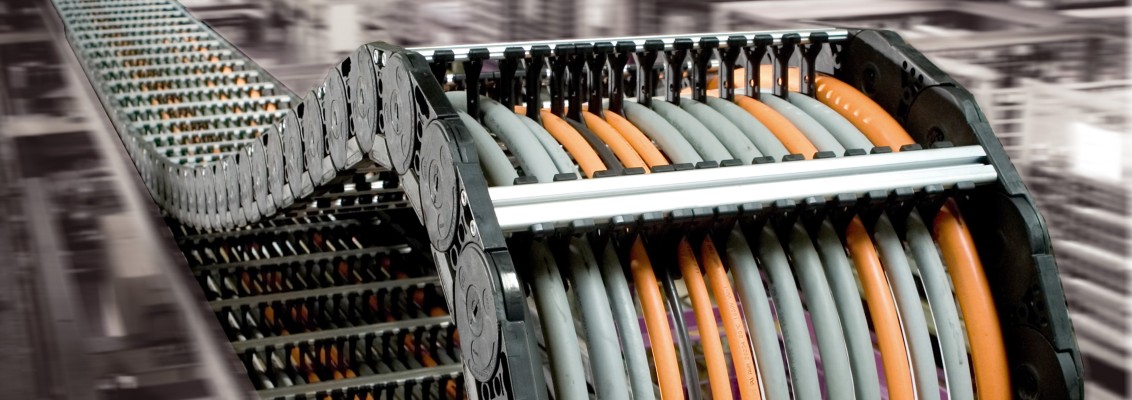
In this second of three Q&A sessions Keith Wilkerson, Business Segment Manager for Robotics and Automation, will discuss some design best practices as well as the common mistakes and failures associated with drag chain installations that he has encountered over the last 20 years at various OEMs and end users.
Q: What is the number one design flaw you see in the field with drag chain applications?
A: As the saying goes, you can’t fit ten pounds into a five pound bag. Many engineers are somewhat designed into a corner. The drag chain is not a high priority component in the design process. But at some point, the cables and hoses need to get from the panel to the X axis over to the Y axis and then on to the Z axis, in the case of a gantry robot. What design engineers are left with may be a physical envelope that does not allow for the proper geometries needed to manage the fill package correctly. Machine repairs and upgrades can be a source of this issue as well. There have been instances where an electrical contractor has fished a PVC-jacketed Ethernet cable through the drag chain on top of a TPE-jacketed servo cable, like our TOPSERV® 650 VFD, completely ignoring the safety factor needed for free movement because “there was room”. Whether the fill package was originally designed with too much content or it happens over numerous machine repairs or upgrades, a drag chain stuffed full to the brim will have a decreased lifespan and much more downtime.
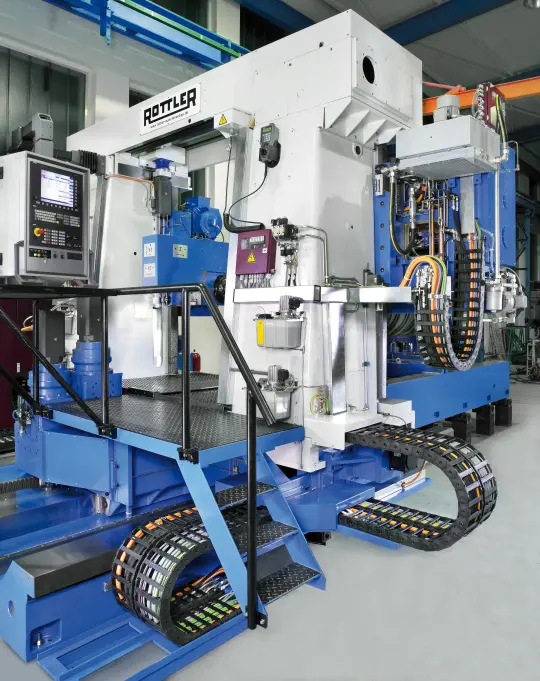
Q: What other systemic design flaws do you encounter in the field?
A: There are several but I’ll only go over a few I see the most in my travels. Uneven weight distribution is the most often design flaw next to an overfill situation. Over time this may lead to the drag chain leaning to one side. This will cause undue stress on the individual links of the drag chain, thus reducing the lifespan of the drag chain itself, especially in a long travel, gliding application. Next on my list is the lack of internal separation. This can cause a myriad of issues. The rule of thumb for separation is to create a cavity with 10 percent safety factor for cables and 20 percent safety factor for hoses. This means if a cable has an O.D. of 20 mm, the inside dimensions of the cavity it travels in should be 22 mm x 22 mm. Adding internal dividers and separators does increase the initial cost of a drag chain, but over the lifespan it will reduce total cost of ownership and downtime. Another systemic design flaw that causes a good share of downtime and failure is the physical placement of each component. Going back to the example in the previous question, PVC and TPE jackets have different levels of abrasion resistance (a.k.a. friction coefficients). Placing dissimilar jacket types next to each other without the proper separation as mentioned before, can cause the cables to possibly bind and wear prematurely. Finally, the last design flaw is one that is a pet peeve of mine. It’s typically found in older drag chains in an MRO situation… zip ties… everywhere. The only “strain relief” needed is at each end of the drag chain.
Q: What are some of the best key practices when designing and building a plug-and-play drag chain solution?
A: I would recommend this above all else; determine what your fill package will consist of first. Even if you are not sure about some of the other parameters the fill package will drive the mechanical envelope the drag chain must operate in. Matching all components properly to the application is another key. An example would be using cables that are rated for an acceleration of 5 m/s² when the real-world acceleration is 20 m/s². Will the cable work? Possibly, but for how long? Confirm the bend radius of the drag chain will accommodate each cable/hose bend radius. Cables that are constantly stressed longitudinally beyond their specified bend radius will fail prematurely. The last one I will mention relates to the use of support and guidance systems, sometimes referred to as guide troughs. These are sort of like a seat belt for your drag chain. They keep the drag chain properly aligned (no snaking), ensuring there is proper support and a uniform, obstruction free path in which to operate.
Q: How important is understanding the acceleration and travel speed when approaching a new design?
A: Acceleration and travel speed is where the rubber meets the road. These two parameters are needed in order to properly select the drag chain type and series, as well as the proper components for the fill package. The end product will not be optimized by simply noting the drag chain “moves fast” or is “fairly slow”. It’s a matter of matching the right components to the dynamic and physical forces of the application in order to create an optimized system solution.
Q: What are some of the best indicators that an end user can look for to determine if their drag chain is beginning to fail?
A: A clear indicator that you may have an issue is when frame stays are missing or appear to be partially unsnapped from its link. This indicator is tricky because it could be a symptom of a deeper, unseen systemic issue. Maybe you have a drag chain that looks “twitchy” as it moves from the retracted to the extended position. I see this issue quite often. The possible causes could be one or more links are beginning to fail or there is debris in the drag chain and/or guidance system. Look for cables that begin to crossover their neighbors or show signs of cork screwing. This is one sign that should be looked at sooner than later, similar to the low tire indicator on your car. These issues should be evaluated by an experienced field support representative to determine your best course of action for repair, redesign or replacement.
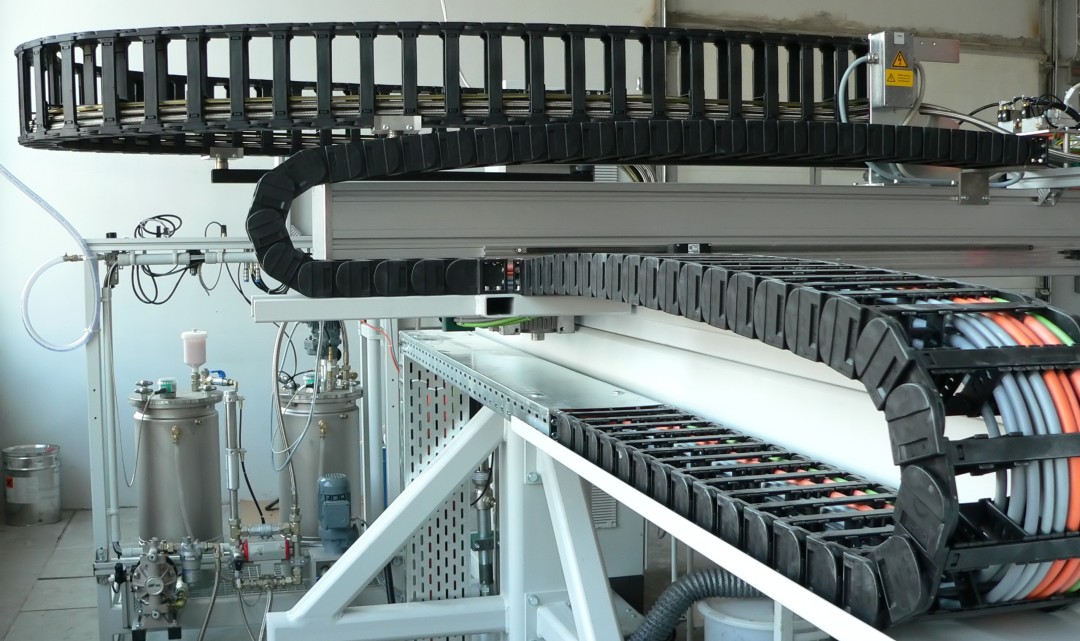
If you would like assistance with a new drag chain design or would like to discuss scheduling a wellness check for a drag chain installed in your facility click here or email us and one of our technical experts will contact you directly.
If you are interested in learning more about HELUKABEL and the broad product portfolio we offer click here for our digital bookshelf.
If you missed the first of the three Q&A sessions focused on cable design for dynamic applications click here .
Click here to read part three of this Q&A With HELU.
ARTICLE DOWNLOAD
Click here to view this article in our digital download center.