Q&A With HELU: Design Considerations for Dynamic Applications - Part 1 of 3
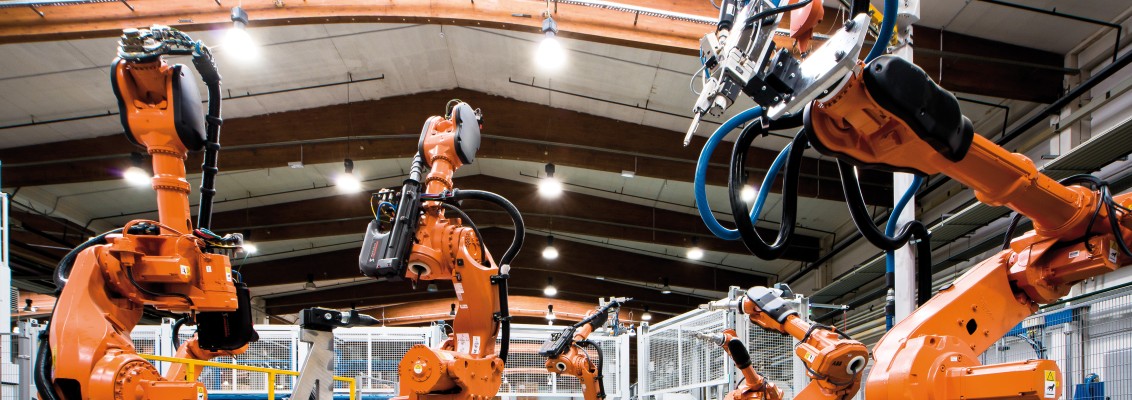
In this first of three Q&A sessions Keith Wilkerson, Business Segment Manager for Robotics and Automation, will discuss some of the key design parameters and challenges cable manufacturers face when developing new drag chain and torsion-rated cable solutions for the ever-changing needs of OEMs and end users.
Q: How are drag chain and torsion-rated cables designed and manufactured differently from each other?
A: In many ways, with respect to the environment each cable will be installed in, they are very similar. Before those details are discussed, let’s talk about the most basic material found in the majority of industrial cables, the copper strand. The key thing to remember is that all copper strands, no matter how they are drawn, how many are used per conductor, or how they are stranded together, have memory. For example, think of a wire coat hanger. If you bend it in a particular direction and then attempt to bend it back to the original position it will not be exactly as it was before. The same applies to copper strands in a multi-conductor industrial cable. This is fine for stationary or fixed applications, but it creates the most basic of challenges for a cable manufacturer when that cable will be bending millions of times in a 2D (drag chain) or 3D (robotic) application. Without giving away too much of how HELUKABEL designs and manufactures these 2D- and 3D-style cables, managing the memory of each strand and conductor plays a major role in design efforts. The more demanding the mechanical application, the greater the cable’s performance characteristics must be. That means progressing from simple bunch or unilay construction for stationary cable to concentric with a short lay length (2D) or concentric with a longer lay length (3D). As the performance needs increase cables also switch from PVC to PP insulation, and to PUR or TPE jacket compounds.
Q: What are some of the cable design considerations for drag chain-rated cables?
A: There are many characteristics to consider and each machine’s drag chains require a full understanding of the application. To design a new cable or recommend a standard catalog cable, your solutions partner should be asking a lot of questions. This will yield the best results. Some of these questions are related to the mechanical parameters - acceleration, travel speed, travel length and cycles per day. There are environmental considerations as well, which include ambient operating temperature, whether the machine is indoors or outdoors, and the presence of chemicals or particulates that may come in contact with the drag chain, such as welding slag or diesel fluid (seen a lot in the wood processing industry). Some of the desired properties of any industrial cable would be a wide temperature range, sunlight resistance, high oil resistance, minimal elongation, high tensile strength, good abrasion resistance, small bend radius, low capacitance and flame propagation. It is possible to produce cables to meet many if not most of these criteria but the cost to produce such a cable would not be accepted by the market. Since a one-size-fits-all is not desirable for most OEMs and end users due to the cost, it is critical to match the best solution based on the overall application with total system cost as a secondary consideration.
Q: What are some of the cable design considerations for torsion/robotic-rated cables?
A: Torsional (3D robotic) cables are required to endure many of the same environmental factors as drag chain cables. As previously mentioned, understanding the entire scope of the application is needed in order to make a proper recommendation or design the best solution. Although the flexing of the cable along its entire length is not present in a torsional application as it is with a drag chain application, there is the added rotational stress applied to the cable. This is demonstrated on an articulated robot when axis four (4) rotates in one direction and axis six (6) rotates in the opposite direction. A cable manufacturer must now consider the memory of the copper strands as it relates to that additional stress. With this in mind, we should understand that the torsional value (+/- XXX°) is one of the most critical parameters of a torsional cable. When comparing cables from various suppliers, use this as the baseline for comparison. A cable that is +/- 180° per meter may be acceptable for a 4-axis palletizing robot, but it may not be best suited for a welding robot in an automotive plant. Also, stating a cable is designed to “withstand torsional applications” is simply not enough to determine if it is the proper solution for the application.
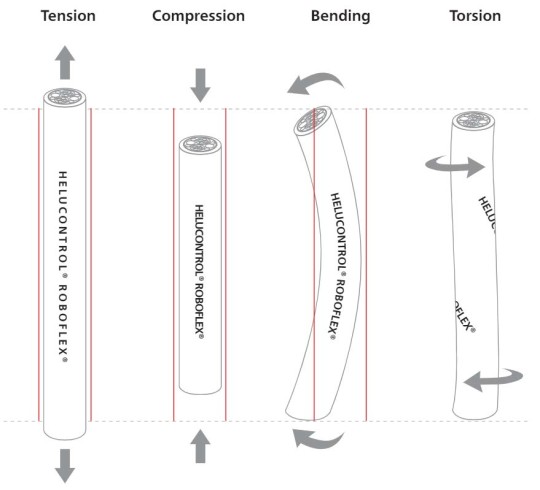
Q: How does acceleration, travel speed and torsion requirements all impact the material selection and or development of new compounds for cables?
A: Cables in highly dynamic applications must withstand acceleration forces up to 50 m/s² and rapid, unforgiving decelerations (the whiplash effect). It seems counterintuitive, but utilizing materials with a certain amount of stiffness is crucial to longevity. If you compare standard tray cable with class 6 stranding to a drag chain-rated cable of the same construction, you should notice the “high performance” cable will seem to have more of a rigid feel even though they both utilize pressure extruded jackets. Choosing the wrong material could increase overall weight per foot and shorten the lifespan of both the cable and the cable management system (drag chain/dress pack).
Q: What are some of the main failures you see in the field for both drag chain cables and robotic cables in dress packs?
A: The majority of dress pack failures, about 85 percent, are cable and hose failures. This ranges from broken strands causing intermittency issues with a fieldbus or control cable to catastrophic failure of the cable at high stress points along the length of the cable. As for drag chain cables, the most common failure is “cork screwing”. We will go into further detail related to these modes of failure in the second and third installments of this white paper.
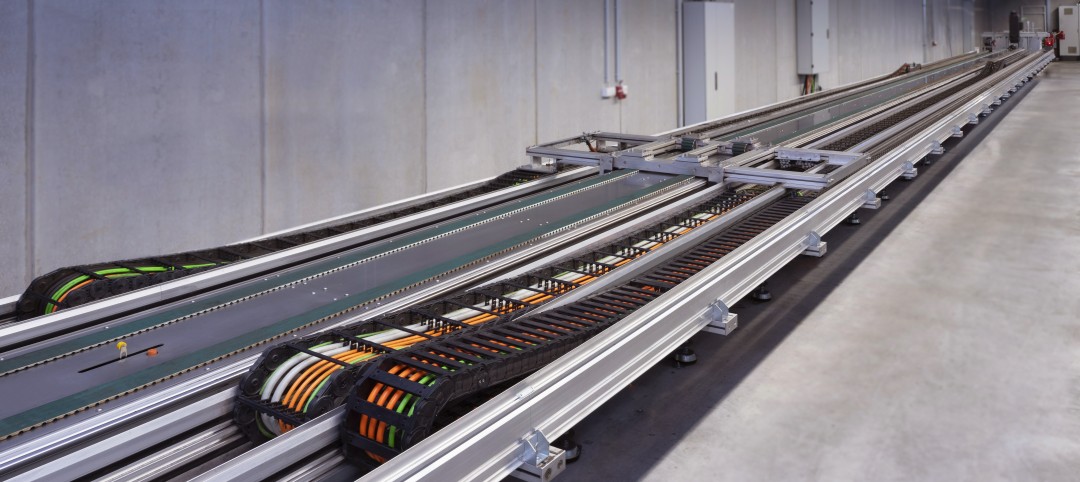
If you have a special application and are in need of a non-standard, application-specific cable click here to be directed to our special cable inquiry form.
If you are interested in learning more about HELUKABEL and the broad product portfolio we offer click here for our digital bookshelf.
Click here to read part two of this Q&A With HELU.
ARTICLE DOWNLOAD
Click here to view this article in our digital download center.